thermoplastic crack cracking test polycarbonate impact|polycarbonate test notched : suppliers Amorphous thermoplastics like acrylic, polycarbonate, Noryl® modified PPO, and Ultem® (polyetherimide) are susceptible to brittle failure when exposed to adverse environmental . Resultado da 16 de out. de 2023 · Marcela Soares - Bella da Semana. Bella da Semana. 79.1K subscribers. Subscribed. 117. Save. 7.4K views 3 months ago. .
{plog:ftitle_list}
30 de mar. de 2023 · Foto: Reprodução. O Brasil registrou, em 2022, 612,9 mil notificações de acidentes de trabalho. O número de óbitos provocados por esses acidentes .
stress cracking resistance
drop testing custom package
polycarbonate test notched
12,000 and PeG-24,000 compounds show no visible signs of cracking or crazing. The polycarbonate specimens show no evidence to stress-cracking when in contact with PVC .polycarbonate has been performed, especially for use in comparison with polycarbonate blends with rubbery particles, but little modeling has been done to understand and predict the .The SEM examination of a typical fracture surface showed that the cracking had initiated within the specimen wall at a local inhomogeneity. The cracking initiated through crazing, and the .
Polycarbonate, an amorphous glassy thermoplastic, is susceptible to cracking or crazing when under stress and in contact with a chemical environment.1 Much of the polycarbonate molded .Amorphous thermoplastics like acrylic, polycarbonate, Noryl® modified PPO, and Ultem® (polyetherimide) are susceptible to brittle failure when exposed to adverse environmental . This investigations deal with that problem and it is shown how the stress cracking resistance of plastics can be influenced according to the already completed product .

The mixed solvent test for polycarbonate is well developed. It involves varying concentrations of n-propyl alcohol as the inert ingredient and toluene as the stress crack . For example, combining polycarbonate material, residual stresses, and machine oil in self-tapping screws or inserts would almost certainly create cracks in plastic parts. The chemical agent does not cause a direct chemical .
drop testing equipment
This study's goal was to apply atomistic molecular modeling techniques to gain a better understanding of the ESC mechanism and to predict the ESC potential of different fluids .the environment all contribute to crack development in stressed polycarbonate. INTRODUCTION Polycarbonate has become one of the leading thermoplastics for medical device use. Polycarbonate, an amorphous glassy thermoplastic is susceptible to cracking or crazing when under stress and in contact with a chemical environment. 1 Much of the• Approximately 25% of all plastic part failures • Not chemical degradation of the polymer . Thermoplastic Creep Behavior: Creep strain increases with: 1,000 psi Load at Various Operating Temperatures . % of Specimens Tested that Resisted Cracking TEST PERIODS 2 DAYS 2 WEEKS 0 20 AVG. MOL. WT. 22,000 24,000 27,000 29,000 0.7% 40 60 80 100 IPA and IPA-containing solutions are common agents used in hospitals to clean or sterilize plastic medical parts. The crack resistance of plastic materials against IPA is, therefore, very important. Figure 4 reveals that the time-to-craze behaviors of RTPU-A and RTPU-B in pure IPA are quite different, especially at the lower range of stresses.
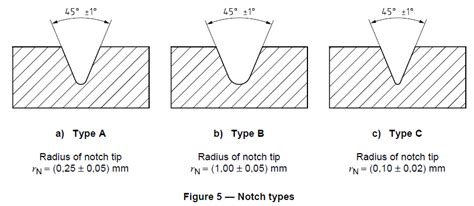
During these tests, the injection molded plastic test specimens were exposed to different environmental media under static bending loads for several weeks and the cracking resistance or crack .Polycarbonate is commonly used in eye protection, as well as in other projectile-resistant viewing and lighting applications that would normally indicate the use of glass, but require much higher impact-resistance. Polycarbonate lenses also protect the eye from UV light.PVC PROPERTIES. George Wypych, in PVC Formulary (Second Edition), 2015. 2.3.12 ENVIRONMENTAL STRESS CRACKING. Environmental stress cracking is considered to be the most frequent mode of failure of plastic materials. 73, 74 It was estimated in 1996 that 20% of plastics failed because of environmental stress cracking. By environmental stress .
Here are some of the top options for impact-resistant plastic sheet for producing quality, durable parts. 1) PC (Polycarbonate) PC (polycarbonate) is a notably durable plastic that can come in a transparent form with a clarity comparable to glass. Because of this and the ease with which it can be manufactured, PC is frequently used in place of .
Soft thermoplastic polyurethane elastomers (TPU) are a class of block copolymers characterised by a low linear modulus (<10MPa), reversible elasticity and excellent abrasion resistance already .
What is stress cracking? And how does stress cracking occur? – When force is applied to plastic, it travels along the polymer chains causing molecules to strain to remain in contact. The polymer chains eventually creep toward the pull and deform. This stage is called creep. With force and time, crazing or stress cracking occurs.
The Gardner test uses a weight that drops straight down onto a rounded, dart-like object sitting atop the material. The amount of weight and height needed to create damage provides the impact resistance. Ultimately, the greater the impact needed to crack the plastic, the higher its impact resistance.
Therefore, the commingled process is still a frontrunner for the production of hybrid yarns consisting of CF yarn and thermoplastic matrix component suitable for the cost-effective and rapid production of high performance thermoplastic composites. 22 The influence of different material parameters such as fibre diameter, 24 thermoplastic fibre . Polycarbonate is trademarked as Lexan or Makrolon. The two major differences between polycarbonate and acrylic are the cost and impact strength. Polycarbonate sheets are 35% costlier than acrylic, and although both materials are way stronger than glass, polycarbonate’s impact strength is unmatched by any thermoplastics available in the market.A company was investigating a rise in cracking of polycarbonate (PC) components used in a conveyor device that was frequently sanitized with disinfectants. The components were reportedly exposed to a disinfectant product containing quaternary ammonium compounds, which have been known to cause environmental stress cracking (ESC) of polycarbonate . Here’s what you need to know about some of the best impact-resistant plastics. Best Impact-Resistant Plastics. At SyBridge, we determine a material’s toughness by looking at the results from its Notched IZOD impact test. This test measures the energy absorbed by a plastic, which helps determine how much energy it can stand before deformation.
Polycarbonate is another material commonly used in luggage construction. Like ABS, polycarbonate is a thermoplastic polymer that is known for its durability and lightweight construction. A. Definition of Polycarbonate. .
Evaluation of crack initiation and propagation, SEM sample preparation takes time, infield inspection not possible, small sample size studied [160], [348] Tap test: Delamination, cracking: Can be used for moisture sensitive composites, simple, inexpensive, insufficient sensitivity for field applications [349], [350] Acoustic emission 6.1 Falling-mass-impact-test results are dependent on the geometry of both the falling mass and the support. Thus, impact tests are used only to obtain relative rankings of materials. Impact values cannot be considered absolute unless the geometry of the test equipment and specimen conform to the end-use requirement. Data obtained by different .Polymer fracture is the study of the fracture surface of an already failed material to determine the method of crack formation and extension in polymers both fiber reinforced and otherwise. [1] Failure in polymer components can occur at relatively low stress levels, far below the tensile strength because of four major reasons: long term stress or creep rupture, cyclic stresses or .
Cycling is a very popular mode of transport and it is estimated that over two billion bicycles are in use [1].But the major concern is the associated head injuries which are common but can be very fatal during an accident [2].Half of the reported deaths and permanent disabilities during bicycling results from the severe head injuries that occurred during the accidents [2], .the samples. Adhesion between polycarbonate and glass were lost in the areas with cracks. The polycarbonate cracking and adhesion loss seemed to occur simultaneously. For smooth glass adherends, no polycarbonate layer cracking was noticed. Table 1: Crack initiation time of adhesive (PC) in-between two roughened glass plates in soaking Soaking .
Polycarbonate (PC) and ABS (acrylonitrile butadiene styrene) are both thermoplastic polymers used for manufacturing applications. PC is typically injection molded or thermoformed into the desired shape. It is used in high-impact applications and where optical transparency is required. ABS is usually injection molded or extruded.
The size of this plastic zone is directly related to the value of the yield stress; a low yield stress will produce a large plastic deformation zone at the crack tip that will effectively lead to crack blunting which increases fracture toughness [Citation 64] and is hypothesized to decrease fatigue crack propagation. Vice versa, an increase in .
c. Polycarbonate. Polycarbonate is an amorphous thermoplastic with a glass transition temperature about 150°C, which shows large strain-to-break and high impact strength properties throughout the normal temperature range experienced by transport aircraft. Polycarbonate not
The investigation of fatigue failure in polymeric materials subjected to cyclic loading holds significant importance across diverse engineering applications. Numerous variables influence material behavior, encompassing material-related factors such as composition, molecular weight, orientation, and additives, as well as external factors like applied stress .Impact Resistance: Compared to polycarbonate, acrylic is more brittle and less resistant to impact. It can crack or shatter under high levels of force. Heat Sensitivity: Acrylic has a lower heat resistance compared to polycarbonate. It can deform or melt when exposed to high temperatures, limiting its use in certain applications.the environment all contribute to crack development in stressed polycarbonate. Introduction Polycarbonate has become one of the leading thermoplastics for medical device use. Polycarbonate, an amorphous glassy thermoplastic, is susceptible to cracking or crazing when under stress and in contact with a chemical environment.1 Much of the
IZOD impact strength is a single-point test in which the impact strength and toughness of a material can be determined. A pendulum with a specific weight on its end will swing down and strike a specimen of a material, and the loss of energy of the pendulum plus the fracturing characteristics of a material are used to set values on impact .
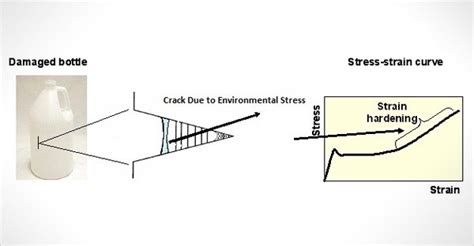
WEBDocumind. Documind is an AI-powered tool that helps users find information in their documents quickly and easily. It offers a range of features that make it a valuable tool for anyone who works with documents, including the ability to upload entire documents at once, chat with PDFs, and build custom ChatGPT from your documents.
thermoplastic crack cracking test polycarbonate impact|polycarbonate test notched